eSource: Equipment Selection for Oil and Coolant Trending Analysis
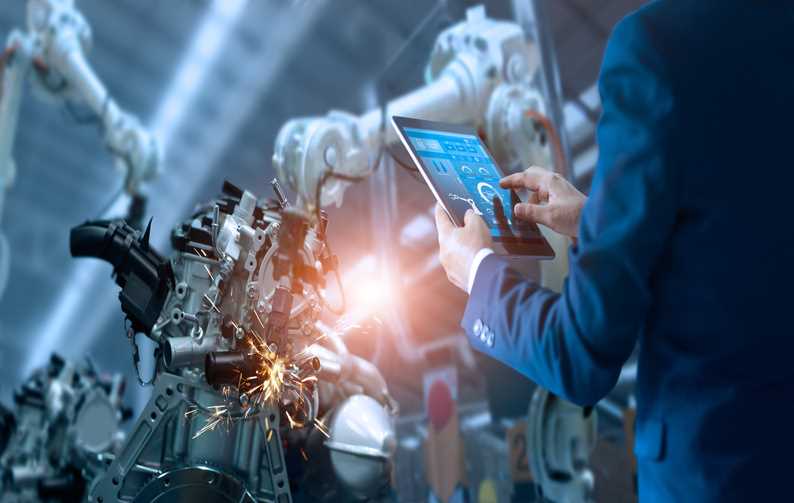
The question is often posed as to which equipment to identify for testing of in-service lubricants and coolants to optimize equipment reliability and plant or fleet health. It may not always be practical to include every piece of equipment as a candidate for including in a testing program. Equipment selection can be done in several steps without feeling that the task is overwhelming. As a rule of thumb, if there is a significant capital investment in equipment then this be a consideration. If replacing equipment is a high capital cost then the asset manager would want to protect this investment. This can then be factored into the failure frequencies and penalty of failure.
A good way to get started is to identify types of failure modes and failure rates of equipment in inventory. This will give you an idea as to what to focus on initially to provide the greatest cost benefit. There is an 80:20 rule, called the Pareto principle, which suggests that the top 20 percent of critical equipment have the potential to cause 80 percent of the problems. Once this information is obtained the reliability of the equipment should be assessed with the penalty of failure if a type of asset or equipment goes down. Even if an equipment asset does not have a frequent failure mode if the penalty of the equipment failure is such that it will cause a significant operational and economic setback to the business it should be targeted for testing of the fluid. How much is bottom line affected due to unplanned downtime, as opposed to scheduled downtime?
Equipment with heavy duty cycles and machinery exposed to more severe environmental conditions, such as dirt, moisture, temperature extremes, should be considered. This can have an accelerated effect on the lubricant and coolant service life. This would also influence sampling frequency.
Equipment age is also a factor to consider. Newer and older machinery usually need more frequent sampling frequencies and experience more frequent service issues than established equipment.
Many times operators will exclude sampling equipment with small sump sizes since the thinking is that it would be easier to just change the oil than to worry about taking a sample. This may be true for the oil condition but it does not provide any monitoring information as to the health of the equipment. If this is a critical piece of equipment this should be taken into consideration.
When taking on a new oil or coolant testing regime do not take on too much at once. When getting started, focus on equipment of particular interest and do not feel every piece of machinery has to be brought on board at the same time. This will allow an opportunity to fine tune internal processes for submitting samples to the laboratory, verify that the selected test package is applicable, and ensures a process for following up on test reports and data is provided. Sometimes it makes sense to focus on the more problematic areas initially and build the program from there. There is also the consideration of safety and how practical it is to obtain a sample. At times due to equipment location or configuration it may be better to apply another condition monitoring practice such as thermography or vibration analysis.
In summary, equipment selection can be listed and graded for priority according to a matrix
• Capital investment
• Frequency of failure mode types
• Criticality and penalty of failure
• Duty cycle
• Work environment
• Machine age
When starting up an analysis program for equipment lubricants and coolants ALS is available to assist in equipment selection and the appropriate test packages. We can work with both your lubricants supplier and maintenance staff. For further information please contact reliability@alsglobal.com