¿Cuáles son los objetivos del mantenimiento predictivo?
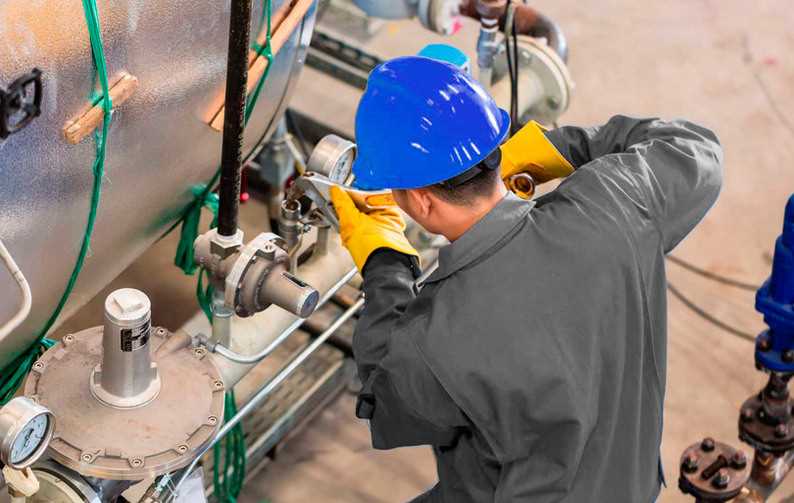
Las industrias y los proveedores de servicios siempre buscan la modalidad de mantenimiento predictivo más adecuada. Y capaz de generar los mejores niveles de disponibilidad, vida útil y productividad de sus equipos.
En los últimos años, el desarrollo de las técnicas de monitoreo y análisis del desempeño y condiciones de los equipos muestra que el mantenimiento predictivo es la mejor alternativa posible para esas empresas.
En este post, vamos a discutir los tipos de mantenimiento existentes, así como los métodos y objetivos del mantenimiento predictivo y sus ventajas en relación a los otros tipos de mantenimiento tradicionalmente aplicados.
Los tipos de mantenimiento
Desde las primeras plantas industriales, el mantenimiento más comúnmente adoptado siempre fue la correctiva. Su principio es bastante simple: una pieza o un equipo roto se repara. En este contexto, no hay ningún gasto continuo con mantenimiento, hasta que la máquina presente fallas y sea necesaria la movilización de equipos de mantenimiento, compra de componentes y paradas de mantenimiento. Esto acaba generando costos muy elevados, exigiendo alta disponibilidad del stock de piezas y, muchas veces, la parada del equipo defectuoso, lo que perjudica el desempeño de la producción.
A continuación se indican los tipos de mantenimiento más comunes a aplicar y cómo se distinguen de los procesos de mantenimiento predictivo:
Manutención preventiva
Entre los tipos de mantenimiento, el mantenimiento preventivo se destaca por mantener el nivel de los equipos, programando intervenciones periódicas para reducir el deterioro de los equipos. Este mantenimiento preventivo combina los métodos basados en el tiempo y las condiciones para mantener el equipo funcionando.
(en el caso de que se produzca un error en el sistema operativo), y en el caso de que se produzca un error en el sistema. pdf "]
A partir de las intervenciones, ésta logra asegurar el desempeño de los materiales estructurales, previniendo la corrosión, la fatiga y otras formas de deterioro. Un factor importante del mantenimiento preventivo es que la inspección o la intervención en el equipo se realiza periódicamente, aunque no presenta problemas.
Mantenimiento de parada
El mantenimiento de parada, también conocido como "mantenimiento por mejora" o "prevención de mantenimiento", consiste en paradas de equipos con el objetivo de hacer que esos alcancen el estado nuevamente. En el mantenimiento de parada, revisiones y reparaciones se hacen en todos los ítems, con el fin de asegurar, con alta probabilidad, un buen desempeño del equipo por un largo período de tiempo.
Mantenimiento correctivo
Como se muestra anteriormente, el mantenimiento correctivo es la forma más común y primordial de mantenimiento. Muchas veces se asocia al ciclo de "rompe-repara". Sin embargo, se aplica no sólo cuando hay efectivamente un fallo o pane (la "quiebra" propiamente dicha).
Cualquier defecto que no haya evolucionado para la falla puede disparar el proceso de intervención. Si se aplica aisladamente, la Correctiva es una de las formas más caras y costosas de mantenimiento, proporcionando baja utilización de las cadenas productivas, disminución de la vida útil de los equipos y paradas completas en momentos inadecuados.
Mantenimiento de rotura
En cuanto a los tipos de mantenimiento planificados, el mantenimiento de rotura está entre aquellos donde no hay planificación de actividades. Esto significa que el objetivo es dejar que el equipo funcione hasta que falle (entre en pane), para luego ser reparado.
El mantenimiento de rotura sólo se puede aplicar cuando las fallas no afectan significativamente la operación, la producción o no generan ninguna pérdida financiera o de seguridad o daño al medio ambiente.
Mantenimiento basado en el tiempo
El mantenimiento basado en el tiempo se resume en inspección visual, lubricación, limpieza del equipo y en la sustitución de piezas para prevenir fallos repentinos y problemas de proceso. Este tipo de mantenimiento generalmente no es complejo, sin requerir especialización, pudiendo ser realizado por los propios operadores después de un entrenamiento básico. El mantenimiento basado en el tiempo forma parte de las actividades de mantenimiento autónomo y del mantenimiento especializado.
Mantenimiento basado en las condiciones
A diferencia del mantenimiento basado en el tiempo, el mantenimiento basado en las condiciones es desencadenado por las condiciones reales del equipo más que por el paso de un intervalo de tiempo predeterminado. La principal herramienta empleada en este caso es el mantenimiento predictivo, y consiste en recoger e informar informaciones que se basan en ciertos valores conocidos de los equipos. Algunos ejemplos son: recolección de la temperatura a través de termografía, análisis de la vibración por la utilización de acelerómetros y análisis de la calidad del aceite en laboratorios.
Con el monitoreo constante, es posible intervenir en los equipos tan pronto como se detectan las variaciones, para corregir las desviaciones antes de que el equipo se rompe. Este tipo de mantenimiento requiere conocimientos técnicos avanzados del equipo y generalmente es tercerizado por empresas especializadas en cada segmento.
Mantenimiento predictivo: qué es y cómo se hace
El mantenimiento predictivo está dentro de la filosofía del mantenimiento basado en las condiciones.
Pero va más allá, teniendo como premisa programar intervenciones en las máquinas, basadas en indicadores de los propios equipos. Estos datos son proporcionados por un programa de monitoreo e inspecciones de rendimiento. Son comúnmente evaluados factores como la vibración, la termografía y otros.
Los principales objetivos del mantenimiento predictivo consisten en determinar por adelantado la necesidad de servicios de mantenimiento, eliminar desmontajes innecesarios para inspección y aumentar el tiempo de disponibilidad de los equipos.
Tal metodología todavía pretende reducir el trabajo de emergencia no planificado, impedir el aumento de los daños y aprovechar la vida útil total de los componentes. De esta forma, su aplicación permite aumentar el grado de confianza en el desempeño de un equipo o en la línea de producción y determinar previamente las interrupciones de fabricación para cuidar de los equipos que necesitan pasar por mantenimiento.
Ejecución del mantenimiento predictivo
La ejecución del mantenimiento predictivo se realiza con la utilización de instrumentos adecuados, capaces de registrar fenómenos, tales como:
- Vibración en las máquinas
- Variación de presión
- Variación de temperatura
- Partículas de desgaste o contaminación...
Después de la constatación y el conocimiento del fenómeno. Se adoptan dos procedimientos: diagnóstico y análisis de la tendencia de la falla que puede ocurrir. De acuerdo con la irregularidad, el responsable tendrá la obligación de establecer, en la medida de lo posible, un diagnóstico referente al origen ya la gravedad del defecto constatado. Este diagnóstico debe realizarse antes de programar la reparación.
El análisis de la tendencia de la falla consiste en prever con antelación la avería o la quiebra. Por medio de instrumentos que ejerzan una vigilancia constante, prediciendo la necesidad de la reparación. Sus métodos de investigación apuntan a averiguar informaciones referentes al estudio de las vibraciones, análisis de aceite, análisis del estado de las superficies y análisis estructurales de piezas.
En este escenario, gana especial importancia el análisis de aceite como herramienta del mantenimiento predictivo.
Mantenimiento predictivo: análisis de aceite
Los estudios permanentes y detallados de los aceites lubricantes utilizados en las máquinas pueden apuntar a anomalías. Los niveles de desgaste de componentes, por ejemplo, a menudo se identifican por la presencia de micropartículas en el aceite. Las contaminaciones por agua o combustibles u otros productos también pueden ser constatadas por el análisis de aceite. Este monitoreo puede orientar acciones puntuales de mantenimiento anticipado, previniendo fallas futuras.
El análisis de aceite se aplica con el objetivo de promover el ahorro de lubricantes y evitar defectos en los equipos. En su aplicación, se supervisan las condiciones de desgaste de la máquina, las propiedades de los aceites y su grado de contaminación.
Echa un vistazo a algunas de las determinaciones más importantes a continuación:
- Metales por espectrometría de emisión atómica (desgaste, aditivación y contaminación)
- Viscosidad (calidad del aceite, contaminación por otros productos)
- Índice de acidez (TAN) (degradación)
- Índice de basicidad (TBN) (degradación)
- Recuento de partículas (contaminación)
- Contenido de agua (contaminación)
- Espectrometría de Infrarrojo: Oxidación, Sulfatación, Nitración y Fuligem (degradación y contaminación)
- Hierro (desgaste y contaminación)
- Índice PQ (desgaste)
Algunos de los instrumentos más comunes en los procesos de laboratorio son los espectrómetros, viscosímetros, tituladores, contadores y microscopios. Con estas herramientas, los análisis van a definir la necesidad y la periodicidad de las intervenciones en la máquina y / o en el propio lubricante.
Mantenimiento predictivo: reducción de costos
Siempre aconsejamos a las empresas que para aumentar la vida útil de sus equipos. Y reducir los costos necesitan estar al día con el mantenimiento predictivo de su maquinaria. Evaluar las condiciones de estos equipos requiere un trabajo minucioso de recolección y análisis de datos de los equipos monitoreados.
El foco del mantenimiento predictivo está siempre en la reducción de costos y en la mayor disponibilidad del equipo. Las herramientas que componen el proceso del mantenimiento predictivo, ayudan a detectar anomalías en los equipos, como su estado de desgaste. Además de informar la presencia de cualquier sustancia contaminante en diversos componentes. De este modo, el mantenimiento predictivo posibilita que algo sea hecho antes que los defectos se agraven, evitando perjuicios mayores.
El mantenimiento predictivo posibilita que las acciones puedan ser tomadas en el momento oportuno. Evitando desgaste de los equipos o pérdida de algún componente importante como consecuencia de alguna falla no identificada o prevenida. Esto todavía proporciona que la maquinaria esté siempre listo para ser utilizado y funcionando con total capacidad, para más productividad. Lo que aumenta la confianza en los equipos.
Conclusión
En este post, buscamos compartir algunas informaciones que muestran la importancia del mantenimiento predictivo para aprovechar lo mejor de sus equipos. En consecuencia, influir positivamente en su producción. Esta gestión es una manera inteligente y eficiente de obtener más disponibilidad y confiabilidad de los activos.
Básicamente, podemos decir que las máquinas "conversan" con nosotros.
Las técnicas de mantenimiento predictivo permiten al experto "escuchar", traducir e interpretar las informaciones que las máquinas nos pasan. A partir de ahí, actuar para obtener de ellas el máximo aprovechamiento, la mejor disponibilidad, con el menor costo y mayor confiabilidad.
Realizar mantenimientos regulares puede hacer toda la diferencia en la productividad de sus máquinas.
Optimice su cadena productiva. Reducir costos en su empresa con el mantenimiento predictivo.
