Desafíos y Soluciones en el Mantenimiento de Equipos de Minería
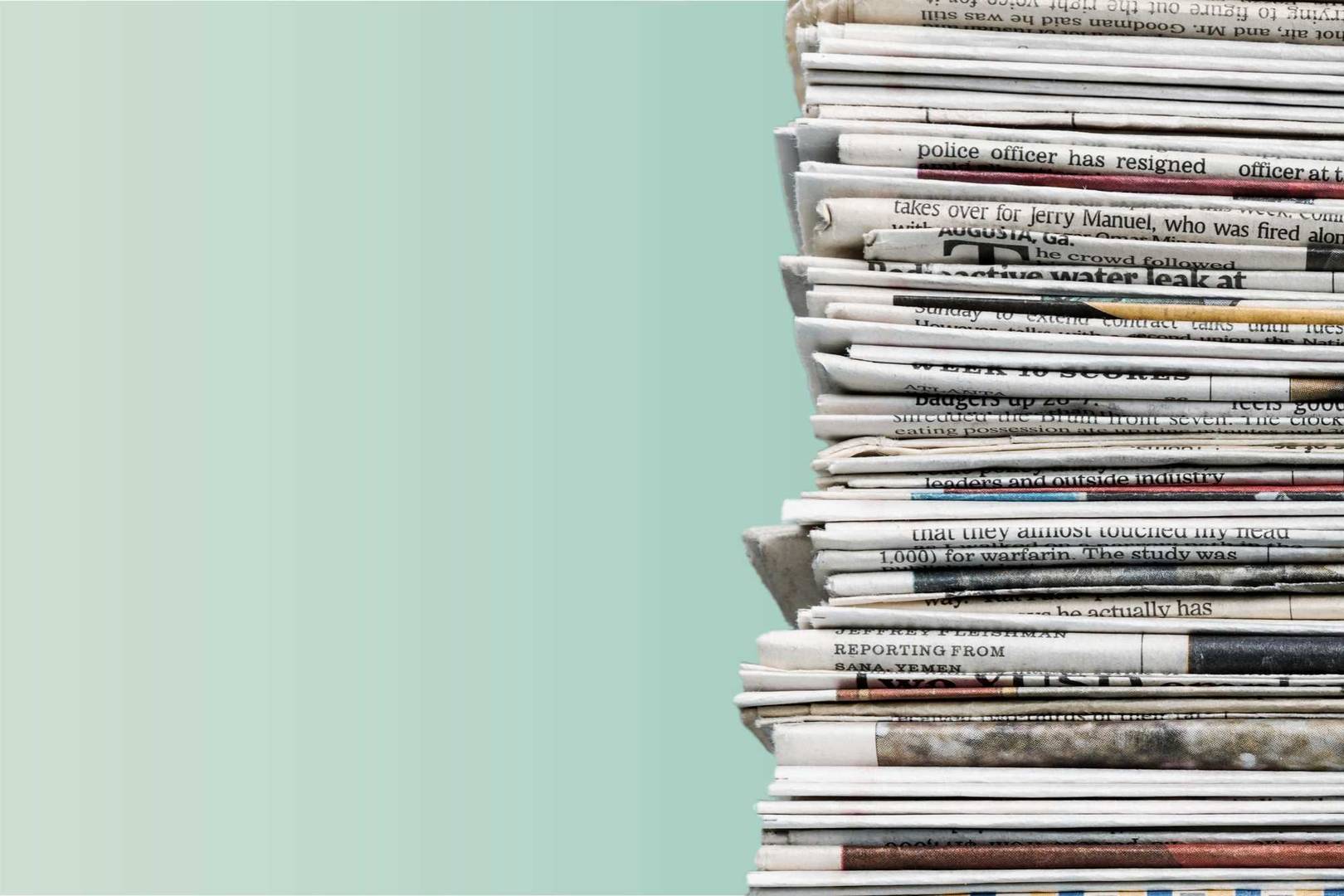
Desafíos y Soluciones en el Mantenimiento de Equipos de Minería
Para permanecer en el mercado, las empresas deben buscar la eficiencia en los detalles. Por lo tanto, se tiende a exigir que el tiempo perdido por averías de los equipos sea lo más breve posible. Para ello contamos, por ejemplo, con el control de mantenimiento frontal. A pesar de ser un elemento imprescindible en una empresa, no todos lo hacen correctamente, pues en ocasiones no cuentan con la estructura o planificación adecuada para su aplicación.
La empresa que tiene un buen control de mantenimiento está a la cabeza en el mercado, pues un control adecuado trae una serie de beneficios a la empresa, principalmente en la productividad y economía de los procesos.
Conozcamos el escenario minero, viendo sus principales equipos y funciones:
Principales tipos de maquinaria pesada
Entre los principales tipos de maquinaria utilizados en la minería, se encuentran:Excavadoras Hidráulicas
La excavadora hidráulica es una máquina que excava, carga camiones y retira material; también puede mover o levantar objetos. Este equipo elimina vertederos, edificios o grandes áreas mineras. La potencia para excavar proviene del sistema hidráulico ubicado en el interior. El aceite presente en el equipo se bombea a los diferentes cilindros, activando la excavadora y convirtiendo la potencia del motor en potencia hidráulica. La excavadora es un equipo versátil, ya que permite el intercambio de su herramienta de trabajo, pudiendo realizar diversas actividades en varios segmentos. Su cuchara puede ser reemplazada por otros implementos, como pinzas, abrazaderas, martillos, tijeras, etc.Cargadoras de ruedas
Este equipo se utiliza para el transporte de cargas de materiales: minerales, tierra, arena, rocas, productos químicos y más. Tiene una buena aplicación en movimientos de tierra, como excavaciones, nivelación y apertura de caminos. Su eficiencia es igual o superior a la de la excavadora hidráulica.
Excavadora
El tractor de orugas está equipado con una cuchilla delantera que puede articular el ángulo de corte del suelo. Es capaz de empujar grandes cantidades de material y se puede utilizar para tirar de otros equipos. Puede equiparse con una grúa para levantar o remolcar, o para romper el suelo.
Mini cargador
El minicargador se utiliza para transportar diversos materiales. Es un equipo muy versátil por su tamaño y puede entrar en espacios reducidos.
Camiones
Los camiones todo terreno se crearon para hacer frente a las duras condiciones que se encuentran en la minería. Pueden ser mecánicos, de diesel, eléctricos y con una capacidad de carga de hasta 400 toneladas.Motoniveladora
La motoniveladora es el equipo utilizado para los acabados finos. Tiene una precisión de menos de un centímetro para su pala. Se puede utilizar en obras de movimiento de tierras pequeñas y medianas, cuando no se dispone de un tractor de orugas. También se utiliza para esparcir materiales y cortar el terreno natural.Rodillo de camino vibrante
El rodillo vibrador tampoco se queda atrás cuando se trata de compactar el suelo. Generalmente, las capas no se compactan con una sola viga. Dependiendo del tipo de material, existe un espesor de capa. Se puede utilizar con una amplitud de vibración baja o alta, lo que define su impacto en el suelo.La plataforma de perforación
Este equipo puede perforar desde pozos artesianos hasta canteras. El taladro puede instalarse como un implemento o montarse en rieles para trabajos grandes.Retroexcavadoras
Esta máquina se utiliza en construcciones urbanas. Las funciones de la máquina son: cavar zanjas para tuberías de agua y alcantarillado, cargar camiones con tierra y desechos, nivelar terrenos, talar muros, entre otras funciones.Confiabilidad y disponibilidad de equipos de minería
En la minería existen varios procesos para la extracción de minerales, que requieren de diferentes maquinarias. Dos de los objetivos de este tipo de actividad son reducir los costos operativos y mejorar la productividad de los equipos.Para ello, es necesario realizar una buena gestión de las máquinas y adoptar un mantenimiento predictivo para un mayor ahorro en gastos.
Los costos, la confiabilidad de la operación y la disponibilidad de los equipos, son aspectos muy relevantes. La monitorización de la máquina permite optimizar estos indicadores.
El mantenimiento regular es esencial para mantener el equipo funcionando al máximo rendimiento. Sin embargo, cada minuto en que el equipo es reparado es un plazo en el que la máquina no está perforando, excavando o transportando mineral. Por lo tanto, estudiar las herramientas de mantenimiento es esencial para que el costo por tonelada de mineral sea más competitivo.
Tipos de mantenimiento
Correctivo
Se enfoca en corregir la capacidad productiva de un equipo, que se ha detenido para realizar sus funciones.¿Cuándo realizar el mantenimiento correctivo?
Lo ideal sería casi nunca, ya que suele ser más caro y puede ser necesario dejar la máquina inactiva un tiempo. Si no se prevé la rotura y no hay repuestos en stock, puede haber un tiempo de espera para la pieza. Por la urgencia, puede terminar pagando más para recibir el artículo rápidamente, sin antes investigar el precio de este artículo.Preventivo
Su foco está en prevenir fallas o paradas de equipos por roturas, y apoyar los servicios de mantenimiento correctivo utilizando una metodología de trabajo periódica.¿Cuándo realizar el mantenimiento preventivo?
El mantenimiento preventivo debe seguir un calendario de planificación que prevea cuándo intervenir el equipo.Mantenimiento preventivo basado en el tiempo: determina la frecuencia con la que se debe realizar el mantenimiento. Es decir que, aunque el equipo no presente fallas, el mantenimiento se realizará dentro del período especificado. Está indicado para máquinas y equipos críticos de la empresa, cuya falla interrumpiría la producción.
Mantenimiento preventivo basado en la productividad: determina cuándo se realizará el mantenimiento de acuerdo con los ciclos operativos.
Mantenimiento preventivo mixto: el calendario tiene en cuenta más de un disparador y el mantenimiento se produce tan pronto como se alcanza el primero, por ejemplo, 6 meses, 1000 horas o 2000 toneladas procesadas.
Predictivo
Es el seguimiento periódico de máquinas, a través de datos recopilados mediante seguimiento o inspecciones. Este mantenimiento permite evaluar la vida útil de los componentes de los equipos y las condiciones necesarias para que este tiempo sea utilizado.A través del mantenimiento predictivo, es posible anticipar la necesidad de servicios de mantenimiento, eliminando la posibilidad de desmontaje innecesario, aumentando el tiempo de disponibilidad del equipo, reduciendo las paradas de emergencia y aumentando la vida útil y la confiabilidad del equipo.
¿Cuándo realizar el mantenimiento predictivo?
Lo ideal es monitorear constantemente su equipo, actualizando su historial y tomando decisiones en cuanto se identifique algún cambio significativo.Sin embargo, para realizar correctamente el mantenimiento predictivo, es necesario recopilar y evaluar los datos de comportamiento.
Para llegar al resultado, periódicamente se monitorean las vibraciones, los fluidos, la temperatura y el rendimiento, con el fin de detectar cualquier cambio. Después del análisis, se estima el tiempo correcto para el mantenimiento o nueva inspección.
Análisis de fluidos
El análisis de fluidos es una de las herramientas más importantes para monitorear el mantenimiento predictivo. Identifica la presencia de partículas en suspensión, el resultado del desgaste de los componentes de la máquina o la contaminación y proporciona algunos otros datos para que su empresa comprenda mejor las condiciones. Existen dos formas de interpretar la información obtenida:Condición del lubricante: se encontró anormalidad en las propiedades físico-químicas del lubricante, o incluso contaminación en el fluido. En ambos casos, la lubricación y la integridad del sistema pueden verse afectadas.
Condición de la máquina: se encontró una anomalía relacionada con el desgaste. Esto se puede detectar por la presencia de varios metales que componen las partes de su equipo. Estos estudios permiten que su empresa pueda ser proactiva en la resolución de problemas.
Principales fallas de equipos en minería
Las fallas de equipos son la principal preocupación de las empresas que brindan servicio de maquinaria pesada. Se realizan numerosos estudios con el fin de minimizar y predecir posibles daños para este tipo de maquinaria, identificando cuáles fallos se producen con mayor frecuencia o pueden resultar más costosos. Algunos de ellos se enumeran a continuación:• Grietas en los haces de resortes.
• Desgaste de los componentes deslizantes.
• Rotura de engranajes de rueda guía en excavadoras.
• Avería de los componentes del motor.
• Grietas en el balde.
• Holgura en los sujetadores de las cadenas de la excavadora.
• Rompiendo el comando final.
Puntos de atención de la flota minera:
Motores
La operación en condiciones severas requiere que el lubricante vaya más allá de la limpieza de las partes móviles y también sea responsable de enfriar el sistema. También es necesario que el fluido selle el paso de los gases de combustión, lo que lo convierte en un gran aliado en la tarea de aumentar la vida útil de los equipos.Transmisión
Este equipo necesita una atención especial por su costo de mantenimiento correctivo y también por causar accidentes mayores cuando colapsa. Es importante que siempre se inspeccione y se le agregue su fluido con propiedades contra la oxidación, corrosión y soporte a la operación a altas temperaturas.Ruedas motorizadas
En este equipo, los engranajes son sometidos a presiones extremas. Un problema común con esta pieza es el micropitting.Análisis fallido
Estos son métodos que se utilizan para prevenir las no conformidades, antes de que se produzcan averías en los equipos. El análisis de fallas tiene dos finalidades: conocer el motivo de la falla, para que se realicen las reparaciones necesarias y con el objetivo de eliminar las posibles repeticiones; y advertir al usuario de posibles daños si el equipo se opera o mantiene de manera incorrecta.Veamos dos casos de fallas de equipos en la industria minera y veamos cómo el análisis ayuda a evitar nuevos problemas y ahorrar en costos de mantenimiento.
Estudio de caso 1 - Fallo operativo - Camión Volvo FMX 500
En una regional, que se encarga del servicio de una determinada empresa minera, se encontraron roturas recurrentes en la viga de resorte.Esta falla provocó una parada prolongada de los equipos que, en lugares distantes, quedó a merced de los concesionarios y sus técnicos. Estos tardaron unos 15 días en llegar al sitio para analizar la causa y otros 10 días para que se enviara e instalara la pieza de repuesto.
La empresa titular del contrato de servicios inició una encuesta, mediante la observación del funcionamiento de los empleados, para localizar un posible error. Después de tres meses de observación constante y rigurosa, se constató que los operarios, en la fase de descarga final, realizaron una marcha atrás con frenado brusco para sacar el máximo de mineral restante de la cuchara ya inclinada. Este movimiento, combinado con el peso de la propia cuchara y la velocidad empleada, concentró una carga excesiva en los haces de muelles que, al transmitir energía, acumularon una carga inadecuada en los últimos haces, provocando la rotura. Una vez identificadas las causas de las fallas, se elaboró un cronograma de capacitación operativa para sensibilizar a cada operador. Con el cronograma fue posible capacitar rápidamente a todos los involucrados y evitar que este tipo de fallas se repita.
Estudio de caso 2 - Fallo del equipo - Unidad de inyección del cargador Cat CAT-966HLRC
Durante el período de garantía de la máquina, se identificó un defecto en una unidad de inyección y se reemplazó. En el momento de realizar el mantenimiento preventivo también se recogió aceite de motor.
El resultado fue crítico, indicando una alta concentración de hierro y níquel, y contaminación por diésel con una caída en la viscosidad del aceite.
Como ya se había realizado la reposición de una unidad en garantía y el equipo volvió a presentar la misma falla, se solicitó garantía para las 6 unidades de inyección. Para ello, se envió el resultado del análisis con la solicitud de garantía. El objetivo de este estudio de caso fue resaltar la importancia de la recolección y continuidad del aceite.
El monitoreo es la mejor manera de evitar altos costos correctivos, lo que permite reparaciones rápidas y específicas.
Conclusión
El control de mantenimiento realizado correctamente redunda en una mejora de la productividad, ahorros en mano de obra y, en general, un mejor costo beneficio con gastos de mantenimiento para la empresa.Invertir en técnicas, estrategias y control de mantenimiento de manera eficiente da como resultado un rendimiento garantizado y el éxito de la empresa.