Case Study: Backup Power Generator
Preventing catastrophic engine failure and loss of production with fluid analysis.
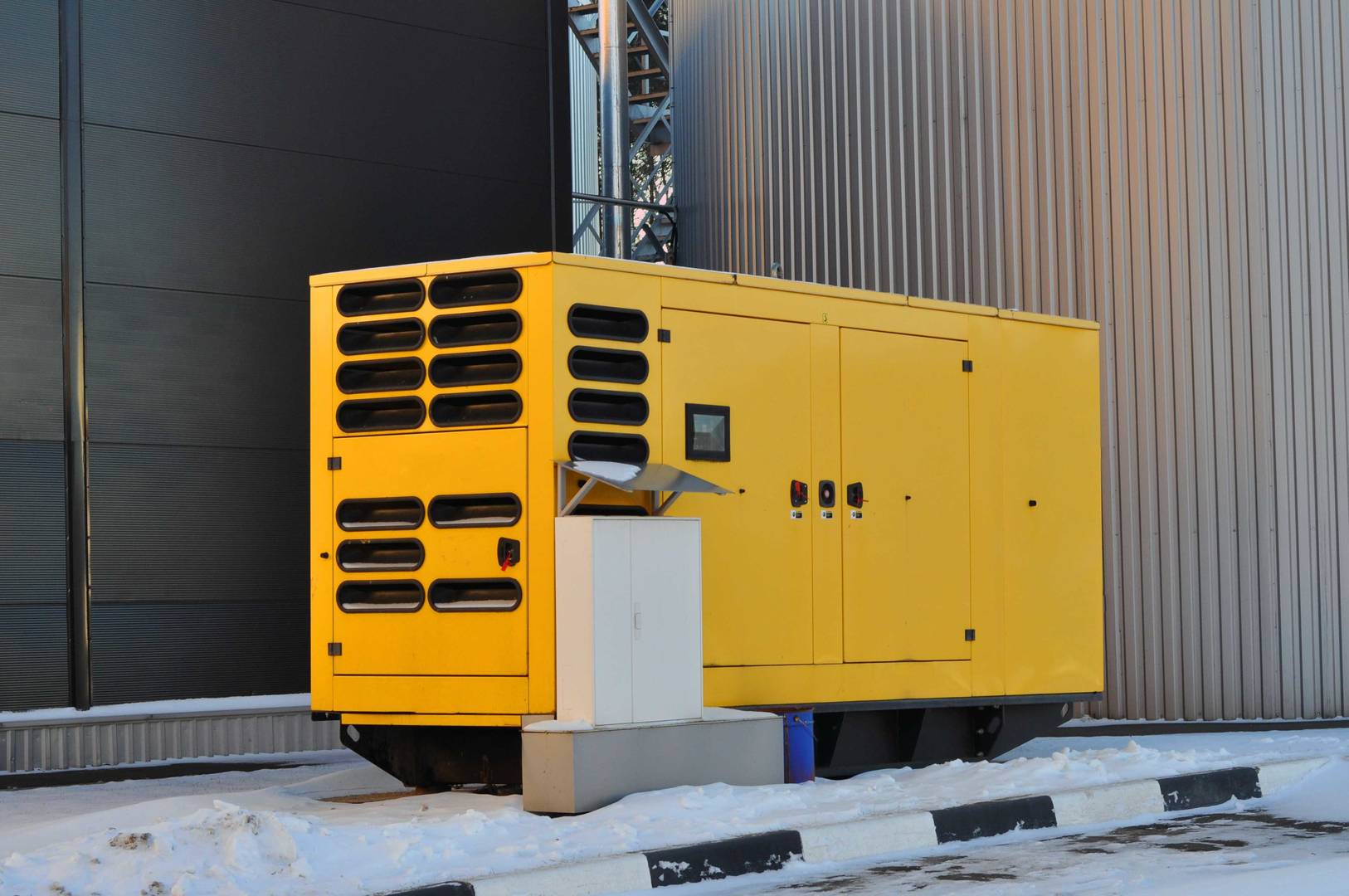
Our customer noticed that his backup generator was showing power loss, abnormal temperature and altered smoke color. As a critical part of their predictive maintenance program and to avoid any further damage to their equipment, ALS was hired to perform fluid analysis. Possible risks to the customer without ALS fluid analysis:
- Catastrophic failure
- Loss of production
- Reduced resale value
ALS has decades of experience delivering equipment reliability services that keep businesses on the right path. These services include equipment failure analysis, initial asset review, predictive analytics, and trend data analysis. The analysis carried out by ALS concluded the sample presented:
- high external contamination by dust (silicon)
- high concentration of iron, copper, chromium, aluminum and excess filings
These findings indicated external contamination that caused engine wear. ALS contacted the customer to suggest detailed inspection actions such as, checking for damage to the seals, condition of the clamps and hoses.
After following ALS' recommendations, the customer found the root cause of the problem was at the entrance of air, highly contaminated by dust, due to poor clamp positioning at the air filter outlet. This caused turbine and cylinder kit deterioration, making it necessary to change the parts. After replacement, the generator was returned to operation.
Without ALS fluid analysis and diagnosis, the cost of external contamination, overheating, internal engine wear, and piston damage resulted in almost 75% cost savings on a potential engine failure expense.
In the above situation ALS fluid analysis and diagnosis resulted in almost 75% cost saving to our customer based on the maintenance/downtime cost to mitigate the causal factor vs the cost of not performing oil fluid analysis and potential catastrophic failure of the generator.