eSource - Selecting Assets for Fluid Analysis and Goal Setting
Whether starting, expanding, or fine-tuning and existing process the information in this article can provide some guidance.
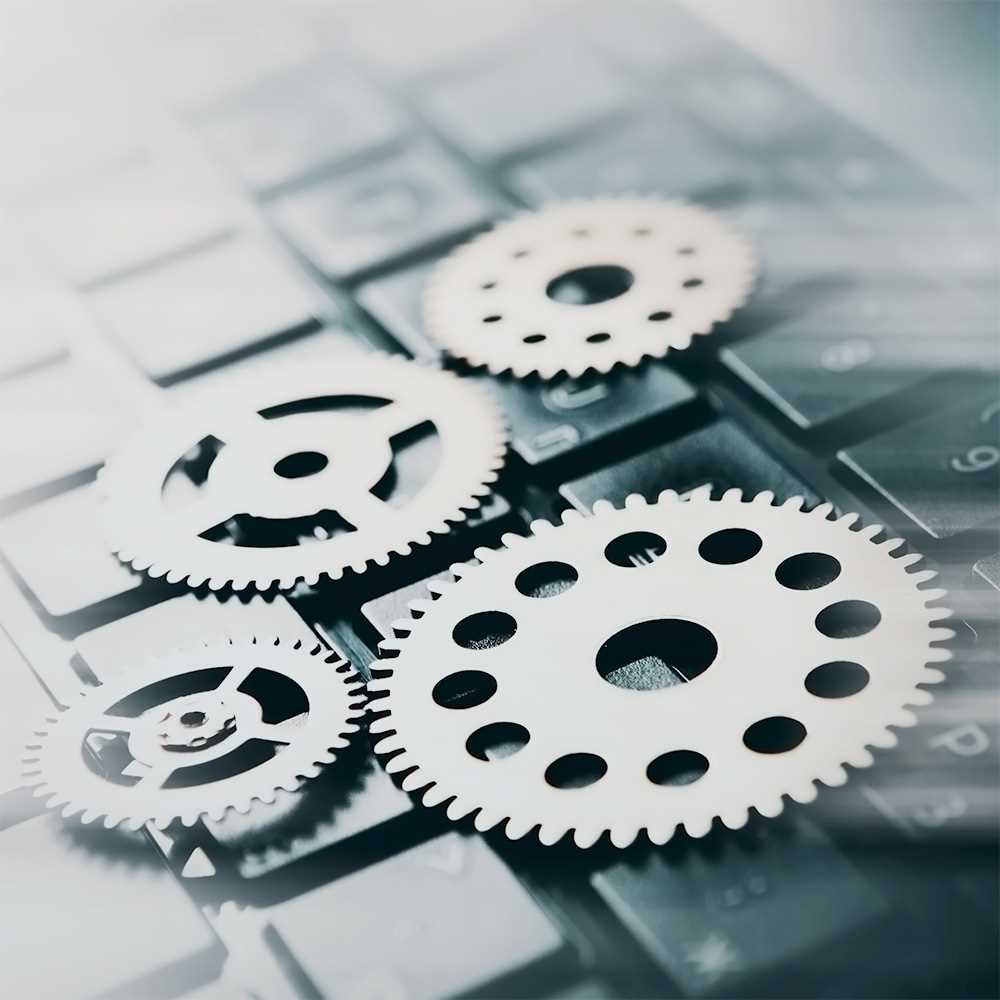
Starting a fluids analysis program can seem daunting as far as what equipment to test regularly and what scope of testing to perform. This can also be the case when reviewing and fine-tuning an existing program. As far as which equipment to select or is currently selected for fluid analysis to monitor equipment and fluid health and reliability, here are some key points to consider.
Evaluate Assets and Work Environment
Evaluate penalty of failure for key equipment. What is the cost of down time during equipment failure? How much capital is invested in an asset? As the interruption to operations increases, or if capital cost of equipment is significant, then the penalty of failure to the business increases. Critical to operation; The 80:20 rule, called the Pareto principle, which in this case suggests that the top 20 percent of critical equipment have the potential to cause 80 percent of the problems.
Review the age of equipment to best tested. New and old equipment usually experience more frequent service issues than established equipment and usually need greater sampling frequencies. This criteria is also applicable to equipment startup after mothballing or extended shutdowns.
Is there a significant investment in capital equipment? If replacing equipment is a high capital cost then the asset manager would want to protect this investment. This can then be factored into the failure frequencies and penalty of failure.
Equipment with heavy duty cycles and machinery exposed to more severe environmental conditions are assets which benefit from a structured fluids analysis program.
Goal Setting
Establish goals and targets for return on investment (RoI) using in-service fluids analysis. Key to using test data for decision making and working towards establishing KPIs (key performance indicators) and relevant tests is working with the testing laboratory, as well as lubricant and coolant suppliers.
Goals and related KPIS for tracking can include:
- Optimizing asset reliability
- Increasing asset resell value
- Reduce capital expenditure by prolonging equipment life
- Optimize fluid life
- Consolidate lubricant and coolant products for improved inventory management
- Optimize maintenance scheduling.
- Replace reactive maintenance and repairs with proactive maintenance. This includes monitoring and managing root cause factors that lead to problems.
Asset Reliability Goals
Asset reliabity management is one half of goal setting. Management of test data in a format that aids in decision making is a critical component of a good fluids analysis program. Use data reporting to identify types of failure modes and failure rates of equipment in inventory. Also, a proactive fluids analysis program can help schedule maintenance based on the actual condition of the equipment as assessed by fluids analysis testing, as opposed to doing routine maintenance on a schedule that may not address optimizing asset reliability. How much is the bottom line affected due to unplanned downtime, as opposed to scheduling downtime based on asset and in-service fluid condition?
Fluid Health Goals
Fluid health and service life is the other half of goal setting. Work with lubricant suppliers to use data to optimize drain intervals: Too soon adds to lubricant and coolant cost. Over-extending drain intervals jeopardizes asset health. Another available benefit is streamlining lubrication and coolant product inventory management.
Data Management and Communication
Once a fluids analysis program has been established targeting critical equipment reliabity and optimizing fluid service life, the next step is to establish effective data management and communication in decision making processes. Take advantage of reporting tools that can be provided by the testing laboratory that streamlines data review and overall health of assets and fluid in service. Manage data for asset reliabity from a fleet-wide or plant-wide perspective, instead of looking at asset reliability from an individual equipment perspective.
Review the Process
Once an effective fluids analysis program has been established and has been performing for some time, periodically review and fine-tune the process if need be.
- Does the current test package support KPIs?
- Are tests being performed that do not add value?
- Establish flagging limits for test parameters that reflect equipment and work conditions for the work location.
- Review root cause monitoring to prevent problems from arising that affect fluid and asset health, contaminants, and environmental influences.
- Communicate with your testing laboratory.